|
July 2006
 King Porkunkhamun I ( 145 - 182 BBQ) - a raised copper vessel
Thanks to my friends on the artmetal project for the seeds of inspiration. To
Alex and her pet burial urns, Chris Ray, Valentin, Kirsten and all the rest.
|
|
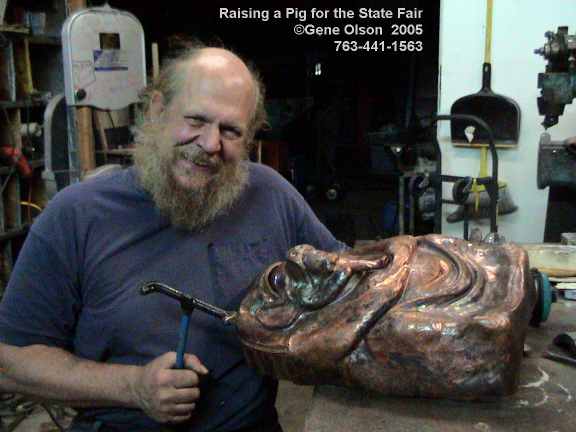
Intitial Thoughts on the project
|
This is about a sculptural vessel that started with a whimsical thought about nature of the burial furniture. My friend Alex makes sculptural urns for pet ashes, and I realised that a pet pig might well end up in a pot instead, so I set about making a suitable vessel to carry this bbq'ed king to his next venue.
The pig is the guest of honor, the focus of adoration. I felt he needed some sort of recognition, a nod to his importance,
like a medieval knight's stone coffin lid, but a sculpted
relief in metal instead. With metal in mind, my thoughts soon shifted to Tut and his gold inner
coffin (shown at left) and I was off and pounding.
I started drawing, piggy laid out with a knife and a fork. I wanted a nice fat
pig and as I was working on an Egyptian motif, I recalled as statue I had seen
of the Pharaoh Akhnauten (Tut's Dad) with his belly hanging out. (right) It was a perfect
match, so I added that detail to the lower half of the lid.
|
|
|
Concept Drawing
A rendering of the idea as a somewhat longer aspect, piece.
The Build
|
|
|
|
|
Gene combined ancient metalworking techniques with modern methods and materials
to produce this sculptural vessel.
The design was mentally unfolded and stretched to provide material where it
would be needed as the drawing was transferred to the flat sheet.
|
The recessed areas were beaten down as the age old process of forming copper
began it’s rhythm, - form, planish, anneal . . . form, planish, anneal . . .
Much of the forming was done in the French manner with hammers over stakes,
though portions were done with modern plastic hammers and the edges were shrunk
with a special tool. Details were added using techniques borrowed from
Japanese and Thracian masters, chasing in detail with small tools over pitch.
|
|
|
Forming metal makes it stiff both from work hardening at a microcrystalline
level and as uneven thickness and convoluted folds and structure on a slightly
larger but still tiny scale. Planishing by hammering or rolling the surface
smooth makes the material uniform and allows one to begin the next stage of
forming with a pristine surface. The planish part went quickly in the early
stages when the piece still fit into the English wheel (kind of a rolling mill
in a C clamp) as the work progressed and the design became more complex it had
to be hand hammered over stakes.
|
Annealing, relaxes pent up stresses and allows the material to move more
freely. The copper is heated to a red heat and then quenched to cool and
shatter off some of the oxides.
The design is restated and reevaluated on the piece at each stage and forming
begins again.
Finally, the detail pieces, fork, knife, apple stem, cobra and beard were
forged and attached; the piece cleaned, sandblasted, and patinated.
|
|
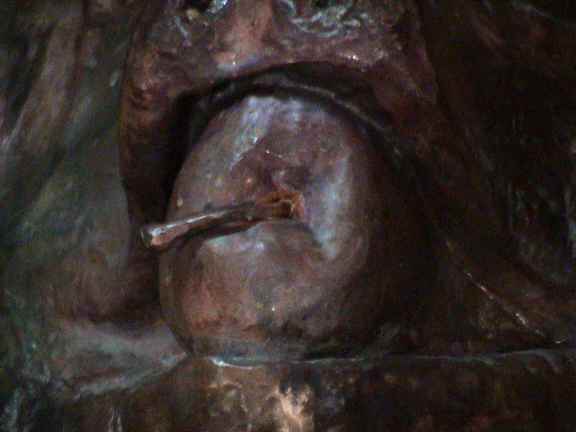
|
|